Case Study - From Manual to Automated: Transforming Multi-Location Fuel Data Collection
How Anovium created a custom hardware-software solution to automate daily pump data collection for a major fuel distributor and c-store operator, eliminating manual processes and transforming operational efficiency.
- Client
- [Private Fuel Distributor]
- Service
- Consulting, Research & Discovery, Custom Development, Hardware Integration, Implementation, Support
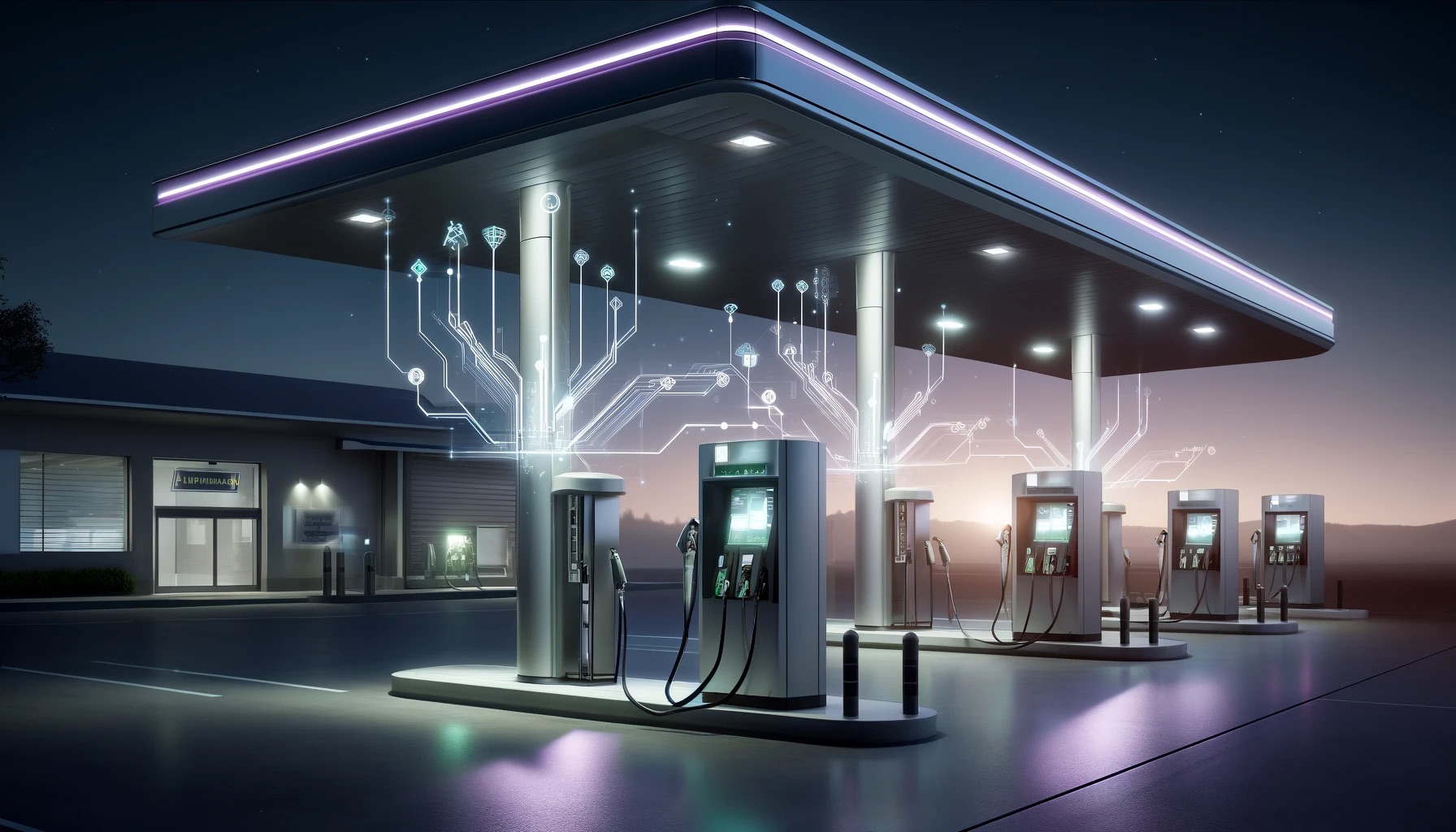
Overview
Managing fuel data across multiple locations presents unique challenges, especially with varying equipment and systems. For our client, a prominent fuel supplier operating over 60 stations across the United States, these challenges were affecting their ability to make data-driven decisions and optimize operations.
Station operators were spending valuable time on tedious data entry from physical pump printouts, creating a burden that took focus away from customer service and store operations. This manual processes was not only time-consuming but also prone to errors, leading to inconsistent reporting and delayed insights for leadership.
Challenge
Our client faced critical operational challenges that couldn't be solved with off-the-shelf solutions:
- Incompatible Legacy Systems
- Manual Data Collection
- Inconsistent Hardware
- Limited Decision-Making Capability
- Inaccurate Reporting
- Data Auditing Backlog
- Compliance Restrictions
The company's leadership was hindered in their ability to promptly analyze trends, monitor sales performance, and make informed business decisions due to delayed and unreliable fuel sales data. Their locations used varying equipment with no universal solution available to bridge these systems. And their manual processes were becoming increasingly problematic as they expanded.
The manual process required staff to physically print fuel data from tank readers and manually enter it into their systems. This approach not only consumed valuable time but also introduced errors and occasionally resulted in missing fuel delivery confirmations, creating reconciliation issues for operations.
Additionally, any solution needed to work within the security compliance specifications regarding the networking infrastructure, adding another layer of complexity to the challenge.
What we did
- Solution Architecture
- Custom Hardware Integration
- Automated Data Collection
- Point-of-Sale Integration
- Real-time Monitoring
Our comprehensive approach began with extensive discovery to understand the specific challenges and existing systems:
-
Deep Discovery & Research
- Consulted with tank monitoring technicians, security teams, accounting teams, operations teams, and fuel dispatchers
- Analyzed security constraints and compliance requirements
- Documented the various hardware systems across locations
-
Custom Hardware Integration
- Modified existing equipment to enable network connectivity
- Installed specialized hardware across multiple states and locations
- Created secure data transmission pathways within compliance specifications
-
Automation Development
- Developed custom software solutions to bridge incompatible systems
- Created automation for data collection that worked around the lack of APIs
- Implemented verification processes to ensure data accuracy
-
Implementation & Support
- Led the installation of networking hardware and computing devices
- Configured software across all locations
- Established ongoing support and maintenance protocols
Anovium's solution eliminated hours of manual data entry while dramatically improving our data accuracy. This wasn't just a technical fix – it transformed how our entire operation functions, giving our management team the real-time insights needed to make better business decisions and allowing our station operators to focus on serving customers instead of paperwork.
Results and Impact
Our solution transformed our client's operations, eliminating manual processes and enabling data-driven decision making across their organization.
- Real-time data visibility
- 100%
- System monitoring
- 24/7
- Manual fuel data entry
- 0
The implementation delivered significant benefits across multiple areas:
-
Enhanced Efficiency and Accuracy
- Eliminated manual data entry, freeing staff to focus on validation and customer service
- Significantly reduced errors in fuel reporting
- Automated detection of fuel deliveries
- Early identification of potential discrepancies
-
Improved Decision-Making Capabilities
- Provided management with accurate, timely data for pricing strategies
- Enabled confident adjustment of purchasing strategies
- Supported accurate confirmation of successful fuel deliveries
- Created visibility into fuel sales patterns across all locations
-
Operational Improvements
- Established goodwill with station operators by removing a long-standing pain point
- Created consistent reporting processes across varied locations
- Improved corporate-station relationships
- Built foundation for future operational innovations
This project demonstrates how Anovium's industry expertise and implementation excellence bridged legacy systems with modern automation, transforming a traditional operation into a data-driven enterprise with enhanced operational visibility and efficiency.